Award-winning site safety
Mitsubishi EDiA fleet enhances operations at Kellogg's Manchester Plant
What was the challenge?
Kellogg's Manchester plant was built in the 1930s and is a huge complex site (the area of 10 football pitches spread over 7 floors), with large numbers of people and many truck movements, often in restricted spaces.
Why this product(s)?
The compact and highly manoeuvrable EDiA electric counterbalance forklift trucks negotiate the various environments with ease and are fitted with many safety features to protect pedestrians.
What was the outcome?
Safety on site has been greatly enhanced without compromising productivity. Importantly, near misses involving pedestrians have been significantly reduced, as has damage to the building and infrastructure.
Follow Kellogg's example
Aware of the dangers posed by large numbers of staff working in close proximity to forklift truck operations, the Kellogg's team worked painstakingly and ingeniously to transform safety at its huge Manchester site. Wherever possible forklifts and pedestrians were separated entirely. Barriers were introduced in any location where forklifts and pedestrians might interact and where separation was not possible, both inside the factory and in the car park. Keen to explore every avenue, Kellogg's worked with the region's Mitsubishi Forklift Trucks distributor, who surveyed the site and identified improvements to Kellogg's forklift fleet.
We worked closely with our local distributor to ensure the trucks made a positive contribution to site safety.
Trucks that actively enhance safety
A fleet of new Mitsubishi EDiA counterbalance and AXiA stacker trucks was commissioned equipped with a wealth of safety features. This included front and rear cameras and GPRS impact detection systems with timed and dated footage, which allow managers to review accidents and identify areas for further improvement. Swivel seats were fitted to improve driver posture when reversing, increasing rear visibility, and reducing driver strain. Speed zoning was introduced to automatically slow trucks down in high-risk areas.
The Mitsubishi EDiA and AXiA trucks have the manoeuvrability for a complex site like Kellogg's, and the safety features provide easy — but most importantly — effective ways to improve daily operations.
Getting the culture right
Underpinning the technologies has been a radical change in the safety culture on site. A campaign was mounted to involve the entire 400+ workforce. Briefings were held, along with toolbox talks. As a result, employees have greater awareness of the need for safety. They are actively encouraged to report incidents and take responsibility for site safety. Managers also conduct safety audits and site walks. Engagement is widespread with all staff invited to share their ideas and learn from each other.
Everyone on site is fully on-board and encouraged to have a say in how we can do things better. Everybody wants to do a good job and be safe whilst doing it. What we have done is to raise awareness of the issues and then give them the tools, training, and techniques to enable that to happen.
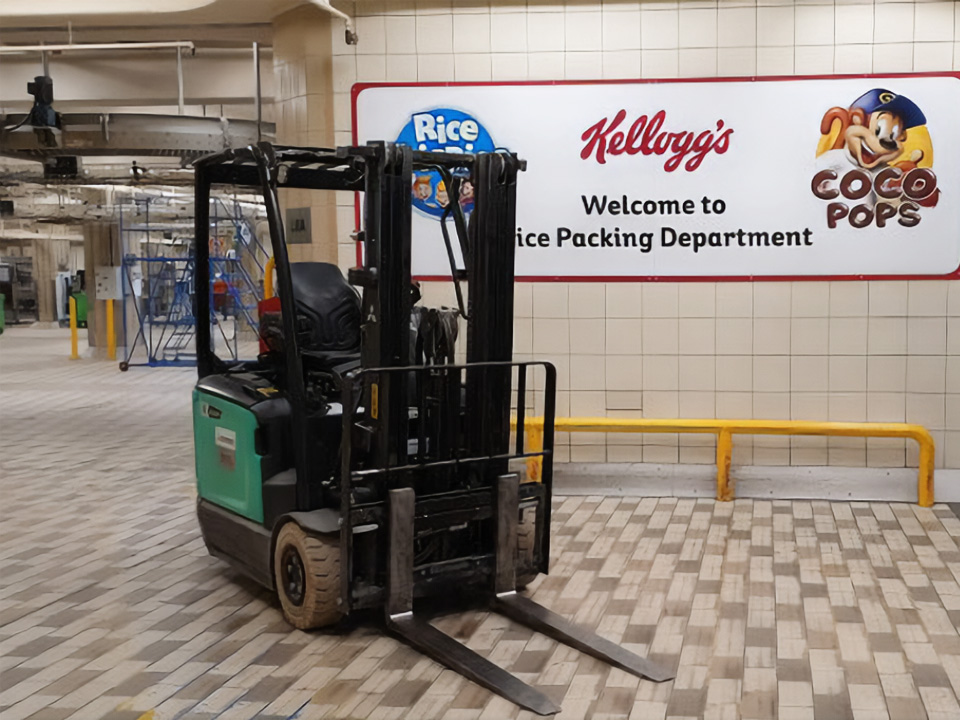
electric counterbalance forklift range
Engineered to deliver maximum performance, while keeping energy consumption to a minimum.
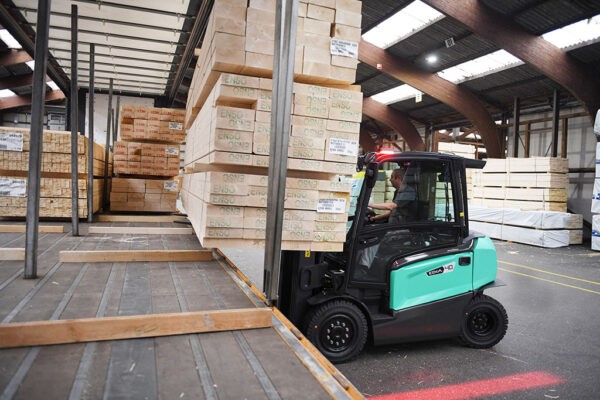